○構想・製作記 |
2007/07/18更新 [New!] | | 試運転開始 ついに試運転できる日がやってきました。 排気試験・トルコン駆動試験・空転試験の後、 レールの上での試運転を行いました。 計2日間、こだま鉄道様の全面的な御協力により実現しました。
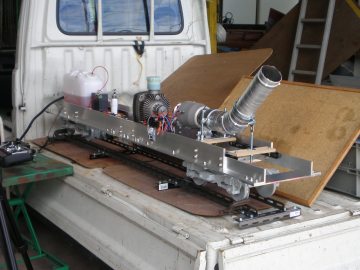 軽四トラックの荷台に設置したところです。 エンジンユニット-トルコンのみにチェーンを張り、 排気試験・トルコン駆動試験を行います。
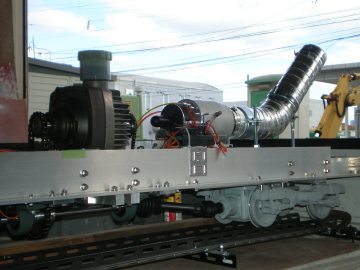 エンジンを始動し、各種予定していたテストをこなしていきます。 製作した排気管の可否は線香の煙を隙間から吸うかで判断できる、 とFoxさんよりご指導いただいており、実際その通りになったので安心しました。 ただ、断熱材がまだ薄いせいか相当熱くなっていましたので、 もう一巻きほど足すべきか検討中です。
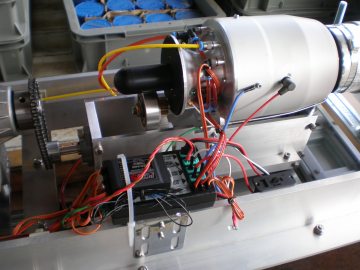 トルコン駆動試験は、 チェーン駆動による振動の程度を知る、 ニュートラル位置の調整、 のために行いました。 振動は特に問題ありませんでした。 ニュートラル位置はサーボシステムを起動し、ロッド長さを調整して行いました。
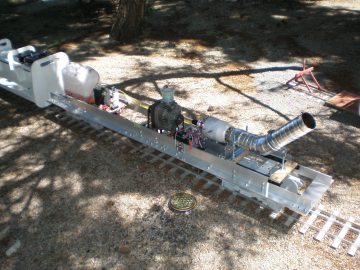 翌日、こだま鉄道KFRに持ち込んでいよいよ走行試験です。 運転操作は、 1.DSCで電波を出さなくしたRC装置でエンジンを始動 2.ディスプレイモニタでアイドル運転確認後、定格回転付近まで上昇 3.トルコン制御ボリュームをセンターより右周りで前進、左で後退 とかなり簡単です。
ついに走行!
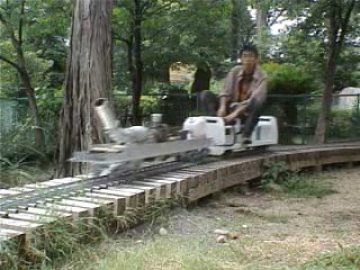 タービン75,000回転に達し、 排気温度に注意しながらゆっくりボリュームをまわしていくと じわじわっと発進していきました。 1周目は超低速、2周目以降徐々に速度を上げて走行しました。 タービンの轟音を響かせながら林間コースを走りぬけます。 その様子を動画でご覧下さい。
動画その1...(始動〜発進〜走行〜停止) 動画その2...(始動〜発進〜通過〜後退)
やっと走行まで漕ぎ着けました、 これからはボデー製作、制御系・電源系の統合と 各所でのデモンストレーションを並行して行っていきたいと思います。
|
|
|
2007/07/17更新 [New!] | | 試運転用仮コントローラの製作 試運転用に、トルコン用のサーボ制御機能だけを持たせた仮コントローラーを製作しました。 運搬,保管時の利便性を考え、コネクタ使用して切り離し出来るようにしました。
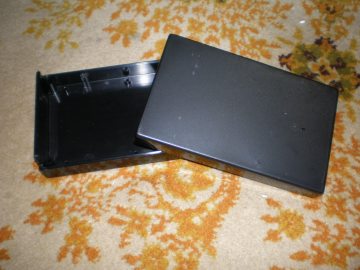 外箱は在庫していたタカチ製プラスチックケースを使います。
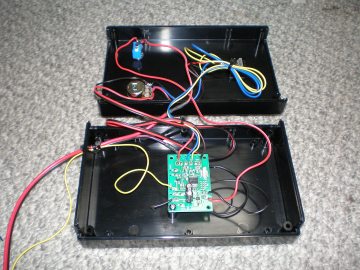 基板,ボリューム,スイッチ類をこのように配置しました。 写真はありませんが、ボリュームはセンタークリックつきものにしてニュートラル位置を固定します。
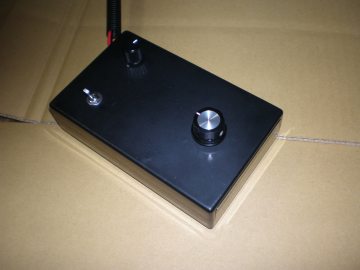 出来上がりました。 センタークリック位置より時計回りで前進、反時計で後退します。 左上にあるボリュームはサーボ動作速度制御用で、 動作速度を抑えることで急激な負荷変動をなくすことが出来ます。 最大出力を伴う加速度試験などを行うとき以外は最も遅い設定にします。
エンジンユニット・補器類の搭載
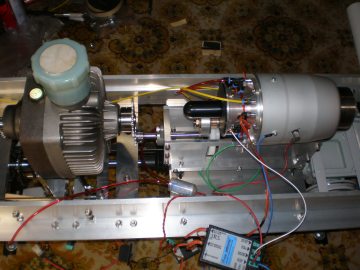 まずはエンジンユニット本体を搭載して ケーブル長さをみながら補器類の配置を決めていきます。
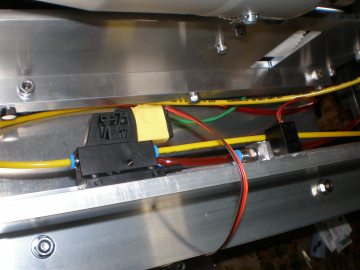 始動ガス及び燃料電磁弁です。 エンジン右側方に配置。
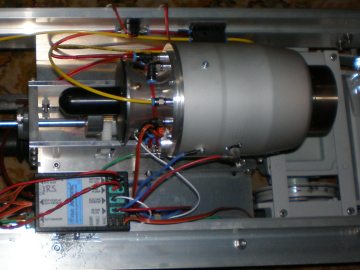 ECUはセンサケーブル長などの理由により、 インテイク直ぐ横に配置。
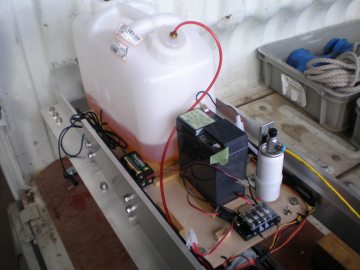 燃料タンク・始動ガスボトル・電源類は熱源から離れた後方に配置。
排気管の製作 設計・部品選定に苦労していたのが排気管です。 排気管はmax700℃に耐え、極力曲りのないものにしなければなりません。 また、エンジン排気ノズルより数ミリ内径が大きいものとし、 その隙間から空気流入するようにしなければなりません。
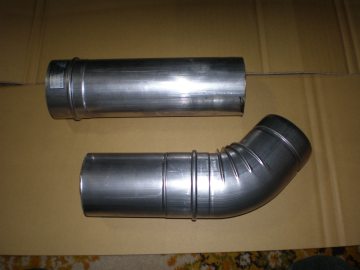 内径80mm,ノズルに程よくかぶる物が見つかりました。 給湯器用吸排気管を製造している『トーセツ株式会社』製KPシリーズです。 これを設計寸法に切断して使用します。 (切断はこだま鉄道本社工場に協力していただきました。ありがとうございます。) ジェット排気をボデールーフより排出するため、 最小限である45deg.の曲り管を使用します。 部品の入手についてメーカーにお尋ねしたところ、 "差し上げます"とお電話いただきました。 大変助かりました、ありがとうございました。
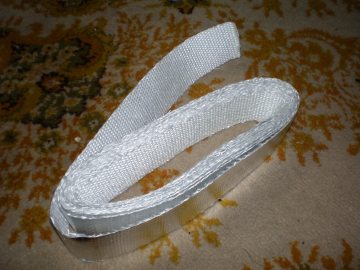 排気管に巻く断熱テープです。 排気管で放熱してしまうと火傷しやすくなってしまったり、 いずれ載せるボデー内が高温になってしまうため、 出来る限り断熱します。 写真は試しに使用する耐熱650℃のグラス+アルミ蒸着断熱テープです。
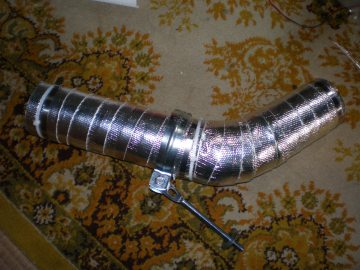 巻き終えました。 排気管支持も市販品です。
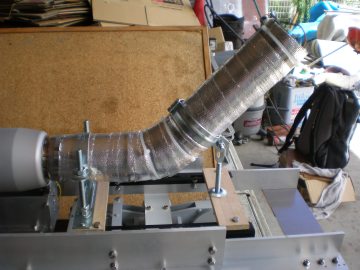 排気管を設置しました。 曲がりが急なのでエンジン始動テストまで少々心配です。
あとはチェーンを張り、試運転を待つばかりです。
|
|
|
2007/07/08更新
| | パワートレインの製作 久しぶりの更新です。パワートレインを中心に製作が進んでいます。
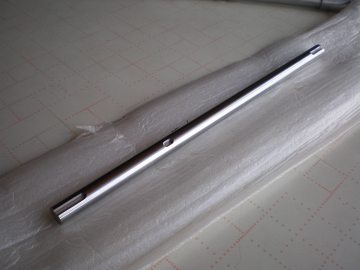 床下中央部を通るシャフトが出来上がってきました。 φ15で両端にキー溝加工をしてあります。 中ほどにはスプロケット固定用にDカット加工指定しましたが、 手違いから極めて短いキー溝になっていまいました。 しかしながらこれでも特に問題ないのでこのまま使用します。 製作は『協栄ホーニング』さんにお願いしました。
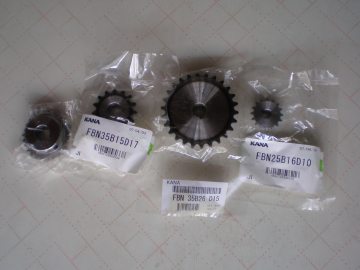 今回使用するスプロケット群です。 エンジンユニット-トルコン→25番 トルコン-ドライブシャフト→35番 それぞれチェーンを使用します。
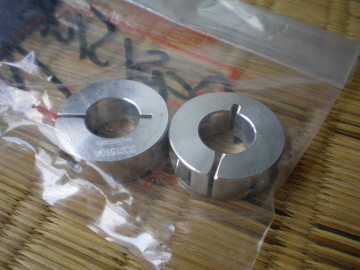 アルミ製シャフトカラーφ15。 シャフトに傷をつけない締付型のカラーです。 スプロケットの軸方向の固定用に使用します。
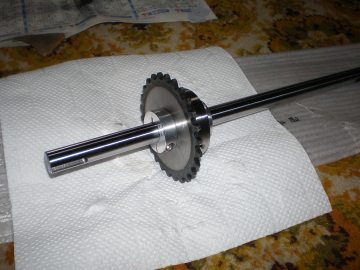 シャフトにスプロケットを装着しました。
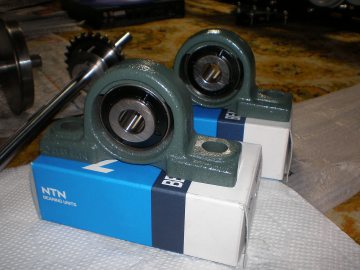 床下でシャフトを支持するピロー型ベアリングユニットです。 呼び名は『UCP202』。
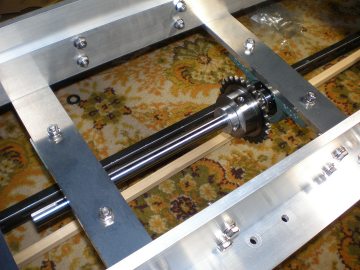 梯子フレームの梁に吊り下げる格好になります。
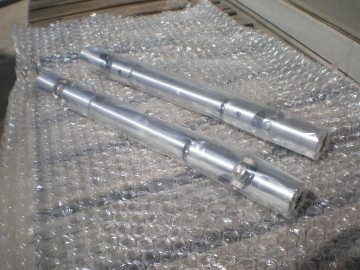 台車と床下シャフトを結ぶユニバーサルジョイントの追加工が出来上がってきました。
 『三好キカイ』製"B-12GX"をベースに、φ15軸孔に追加工したものです。 ジョイント首振角は30deg,スライド量は70mmあります。
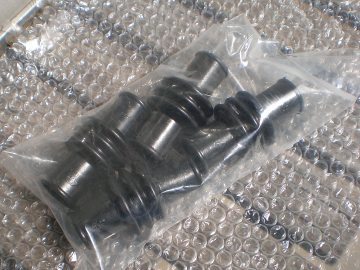 ジョイント可動部の防塵に、ブーツを装着します。
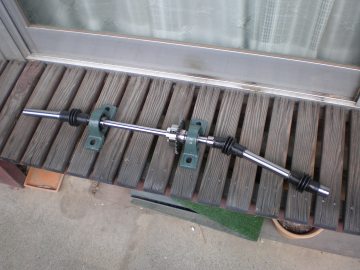 フレームへ組み付ける前にシャフトとジョイントを結んでおきます。
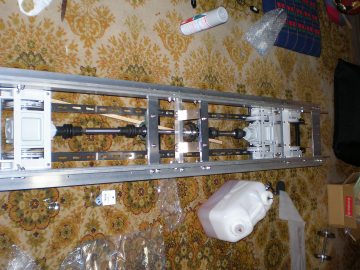 フレームへ装着。 これでシャフトと台車ギアボックスとが結ばれました。
トルコン及び制御関連部分の製作
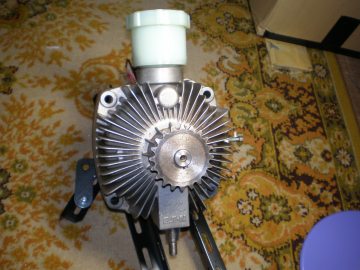 今回の動力伝達の要、トルコンです。 メーカー廃業、絶版品でしたが、『モデルニクス』さんになんとか探していただきました。 しかし設計と逆回転入力仕様しかみつからかなかったため、 以前のキハと換装し、キハに逆回転エンジンを搭載することで問題を解決しました。 このトルコンで無断変速及び逆転を行います。 コントロールはレバー1本で、軸配置も非常に使いやすいものになっています。
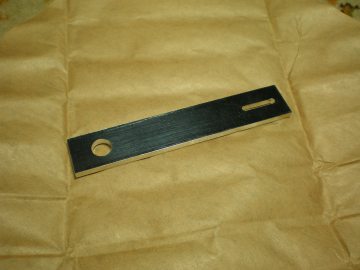 サーボでのトルコン制御に用いるレバーです。 アルミ製で、リンケージロッドのストローク調整用に長孔があけてあります。 レバー可動範囲は前後進各13deg.です。 これも『アルミプラス』さんにお願いしました。
○リンケージロッドの製作 トルコンをサーボで制御するためのロッドを製作します。
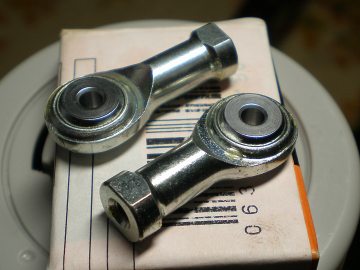 リンケージロッド用のロッドエンドです。 『THK』製"NHS3T"M3仕様です。
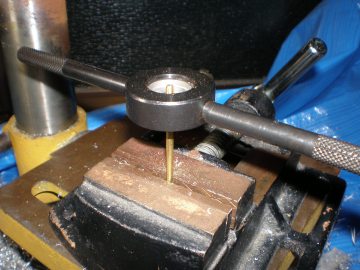 真鍮丸棒両端にM3雄ねじをきってロッドにします。
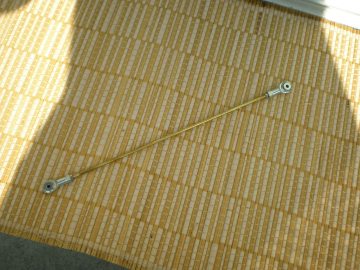 ロッドエンドをねじ込んでナットでとめれば完成です。 全長を15mm程調整できるようになっています。
○トルコン及びサーボの搭載
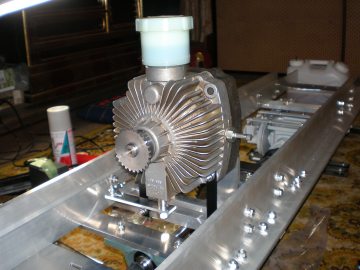 フレームにトルコンを搭載。
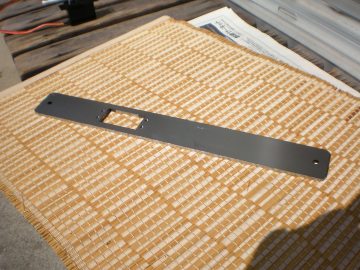 サーボマウントです。 3.2tSSミガキ鋼板からレーザーカットで切り出してもらいました。 小孔4つはM3タップ加工、表面はクリア塗布を行ってあります。
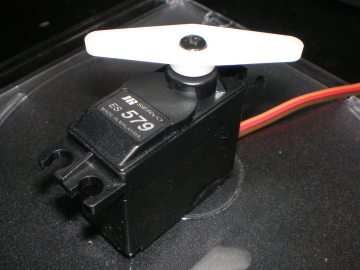 今回テスト段階で使用するサーボです。 『日本遠隔制御』製"ES579"普及型モデルです。 6V使用で9.5kg・cmのトルクがあります。 トルコン制御レバーは動作角速度(負荷)によって必要トルクが激しく変動するため、 サーボの選定には苦労しました。 動作速度はサーボコントローラで制御できるため、 出来るだけ遅く設定し、エンジン及びサーボに瞬間的な負荷増大が起こらないようにします。 テストにて能力不足が判明した場合、上位機種の高トルクモデルに換装します。
 サーボマウントに収まったサーボ。 サーボには大型のサーボホーンを装着してあります。
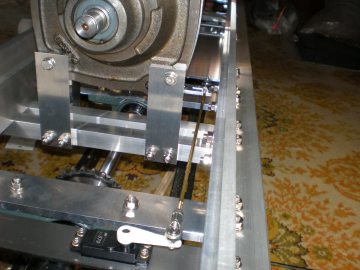 サーボ・マウントを搭載し、トルコンレバーとリンクさせました。 今のところサーボコントローラにトリム機構がないため、 ロッド全長でニュートラル調整しています。 |
|
|
2007/05/12更新
| | DT74タイプ台車2つ目 やっと2つめの塗装に取り掛かることができました。
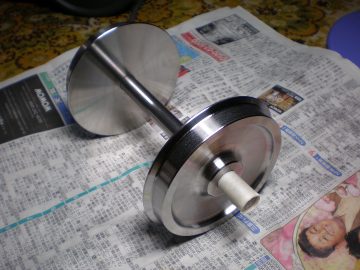 各部品を脱脂・マスキングをして塗装に備えます。
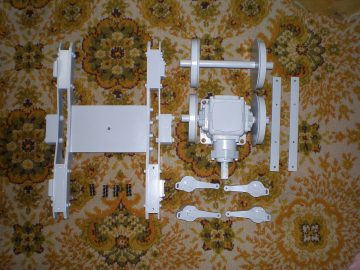 各部分ごとに、 プラサフ→本塗り→クリア→ミガキ を行いました。
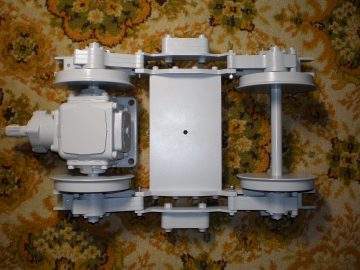 台枠に軸梁・車輪・ベベルボックス等を組みつけていきます。
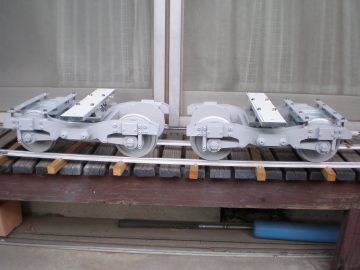 最後にボルスタを装着して組みあがり。 これで台車が揃いました。
|
|
|
2007/04/18更新
| | PJ-Wターボシャフトエンジン試運転 エンジンについてお世話になっている『フォックスコーポレーション』さんに行って初火入れを行ってきました。
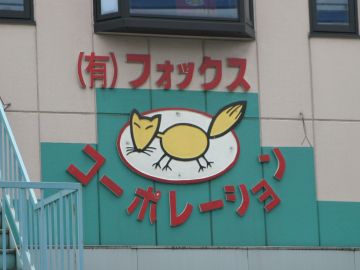 エンジンの試運転、各種取り扱いについてご指導いただくため行ってまいりました。 フォックスコーポレーションさんは神戸にあります。
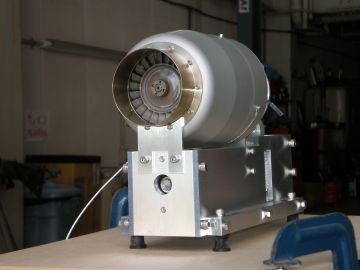 エンジンユニットをテストベンチに固定します。 配線・配管作業もしていただきました。
 燃料系の配管です。 赤色が主燃料、黄色が始動用燃料(ブタンガス)です。
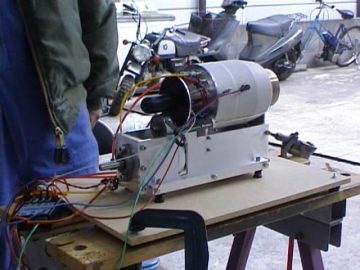 説明を受けながらいよいよ火入れです。轟音とともに回転があがっていきます。 まさに本物ジェットサウンド! フォックスコーポレーションのスタッフの方々には大変丁寧にご指導頂きました。 ありがとうございました。
<動画>試運転の様子はこちら
|
|
|
2007/04/14更新
| | メインフレームの製作開始 久々の更新です。設計や、他車両のコントローラ開発に時間をとられていましたが、 やっと製作にかかることができました。 構造はキハ8500と同じく、Lアングルとフラットバーをはしご状に組んだものにしました。 できるだけ軽くしたいため、アルミ合金(6063,2017)を用います。
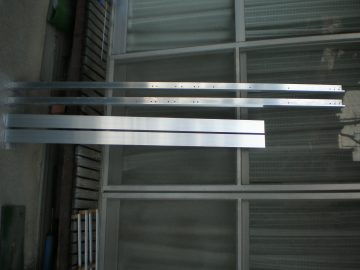 材料を調達してきました。 A6063等辺アングルと平角材です。 再び『ニッカル商工』さんにお願いして指定寸法に切断後、納品していただきました。 尚平角はアングルのサポートとして使用します。
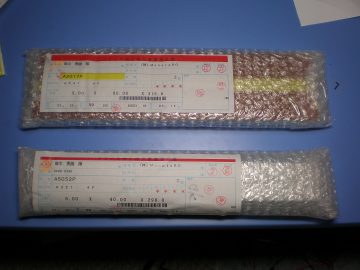 枕木方向に組む平角材です。 定尺購入から切り出すのでは残材が多く、費用も高くつくため 今回はフリープレートを使用しました。 A5052,A2017(ジュラルミン)の4F仕上げ品です。
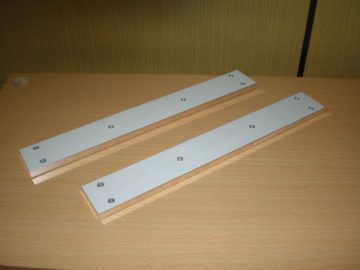 設計図面に従い、孔加工していきます。 写真の部品は床下シャフトを受けるベアリングユニットの台座も兼ねます。
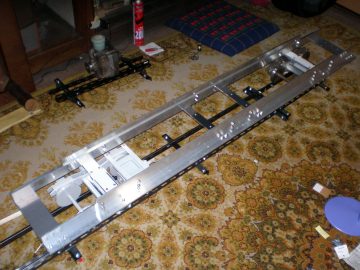 孔明け加工が終わり、はしご状に組みました。 早速台車の上に乗せて様子を見ます。
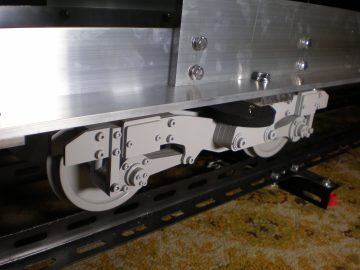 台車にフレームが乗っかるだけでいきなり車両になる気がします。 当たり前ですが...。
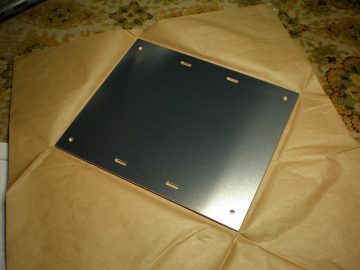 エンジンユニットベースです。 この上にエンジンユニット本体が固定されます。 これも『アルミプラス』さんに加工をお願いしました。 長孔が開けてあるのは、チェーンテンション調整のためです。 素材はA5052プレート4.0tです。
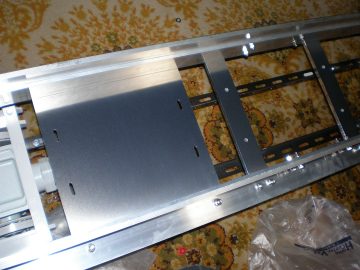 ベースはフレームに直付けです。
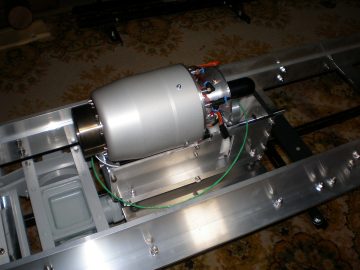 エンジンユニットを載せてみました。 枕木方向に問題なくスライドできました。
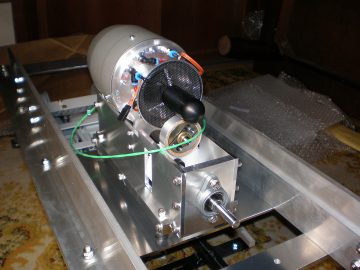 |
|
|
2007/03/02更新
| | 新台車試作5
○動力台車化
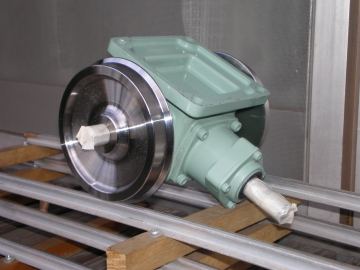 ツバキエマソン製ベベルギアボックスにφ102車輪を圧入してあります。 モデルニクスさんに作っていただきました。
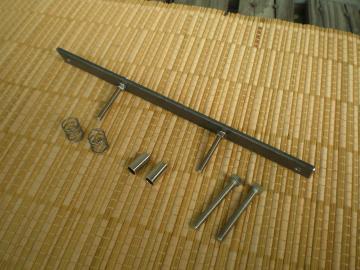 動力台車化に必要な小物部品達です。 もともと動力台車として設計していますので、 これらを組めば直ぐ完成です。
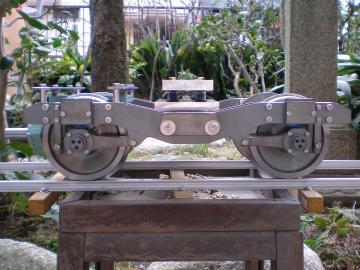 組み込みが完了しました。
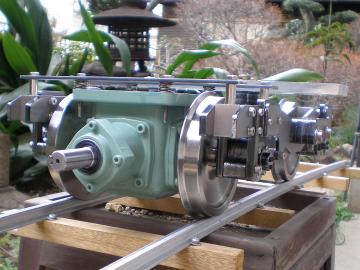 ギアボックス後方から。
○塗装 少々錆が浮いてきましたので早急に塗装することにしました。
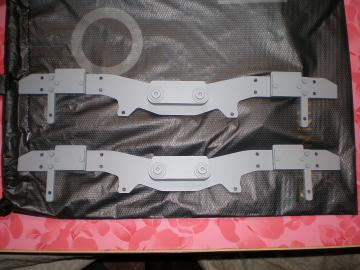 各モジュールごとに分解して塗装することにしました。 錆をサンドペーパーで落とし、脱脂後自動車補修用プラサフを塗布しました。 表面がざらつくので1000番のペーパーで均してあります。
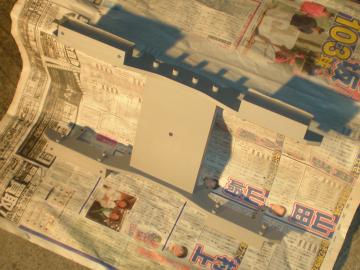 主台枠はアルミが使ってありますので、最初にアルミ用プライマーを吹いておきました。 この後市販のアクリルラッカー『ライトグレー』を塗布、 コンパウンドを使って磨いていきました。
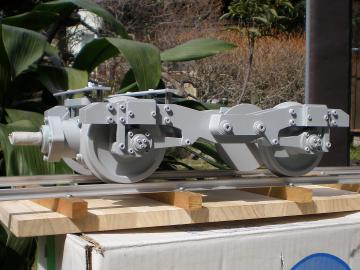 ※この画像はクリックで拡大できます 塗装が完了しました。 ライトグレー1色なのでちょっと味気ないですが、 アクセサリーパーツなどを付けていけばよくなるでしょう。
 ※この画像はクリックで拡大できます 見える面は映りこむまで磨いてありますが、 色が色だけにあまりきれいに見えません...。
これで台車が使えるようになりました、 が、まだもう1つ作らねばなりません...。 |
|
|
2007/02/24更新
| | 新台車試作4
部品が揃ってきたので加工・組み立て開始です。
○軸箱・アクセサリ部品追加工
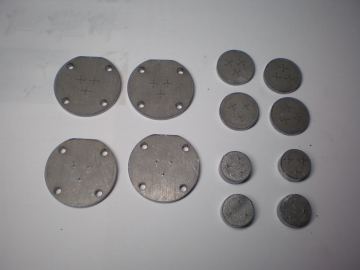 レーザーカットが苦手な部分(小径孔、タップ下穴等)がありますので、 そこは手持ちの工具で追加工していきます。 写真は加工が必要な軸箱関連の部品群(1台車分)です。 孔位置はマーキングしてもらいましたので、まずはポンチ打を行いました。
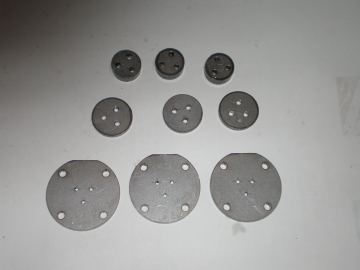 穴あけが終わりました。 小さいのがM2下穴、ひと回り大きいのがその通し孔です。
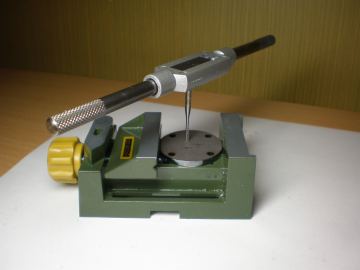 M2タップ加工をしています。
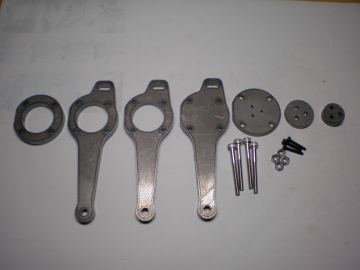 これらの部品で1つの軸箱(スイングアーム)を構成します。
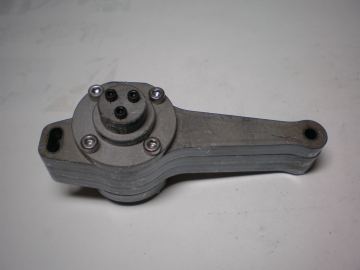 組みあがりました。 細かいところは実車と異なりますが雰囲気だけは出ているのではないでしょうか。
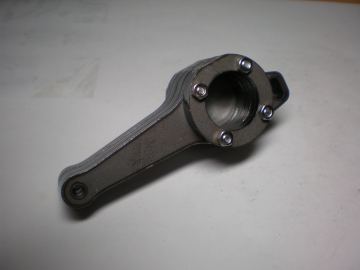 裏面から。 ここにニードルローラーベアリングを挿入します。
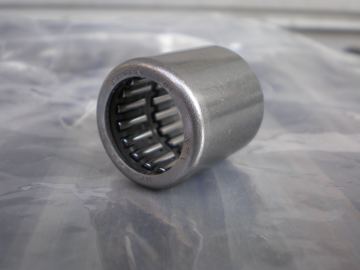 今回使用するベアリングです。 『NTN』製"HK1522ZWD"ニードルローラーベアリングです。
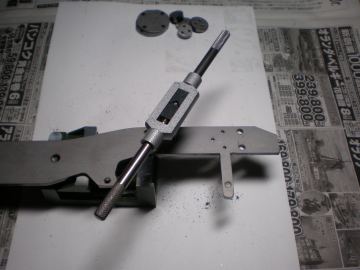 外側フレームにもアクセサリを取り付けるためのタップ加工をしていきます。
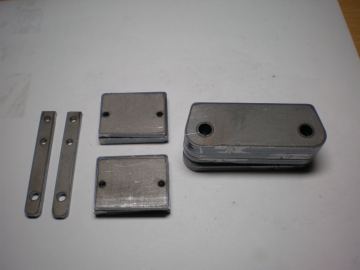 外側フレームに取り付けるアクセサリ部品です。
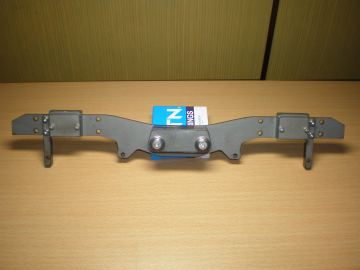 フレームに取り付けました。 これらの正式名称が分かりません...。
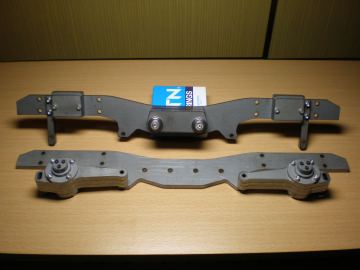 加工が終了した部品、片側分です。
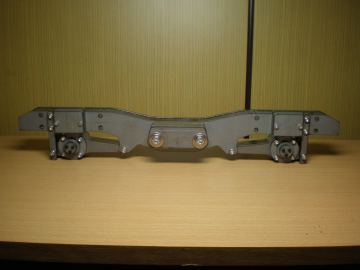 仮組みをして可動部分の動きをチェックします。 少々渋いところがあったので、鑢と砥石で滑らかに動くよう削りました。
○総合組み立て
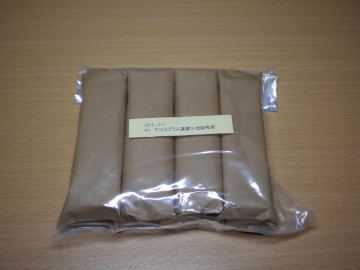 内側・外側フレームに挟まれる形で使用する部品と、 H枠の横梁の加工をまたまた『アルミプラス』さんにお願いしました。 毎度芸術品のような梱包で送ってくださいます。
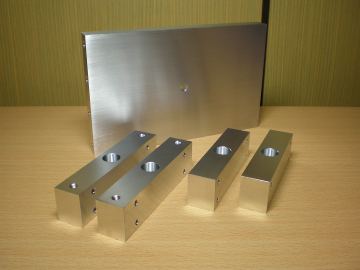 毎度惚れ惚れするような出来栄えです。
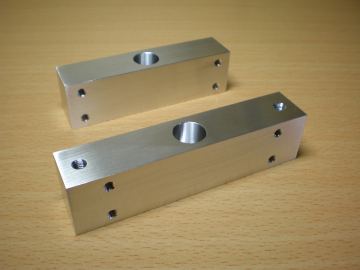 これらを内・外フレームの間に入れて、スイングアームをポケット孔に挿入したバネで受けます。 奥は付随用、手前の長いのは動軸用で、ベベルボックスを受けるためのタップが立ててあります。
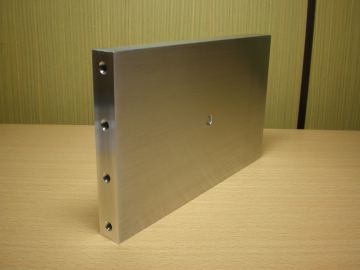 これで台車にかかる全ての荷重を受けます。 厚さは15mmありますが、アルミのため随分軽いです。
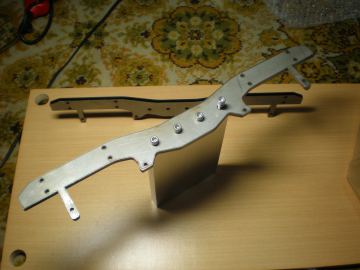 早速組み立てに入ります。 まずは横梁(?)に内側フレーム(6.0t)を固定していきます。 通し孔もぎりぎり寸法でしか明けてありませんが、 レーザー加工+プロの加工でばっちりです。
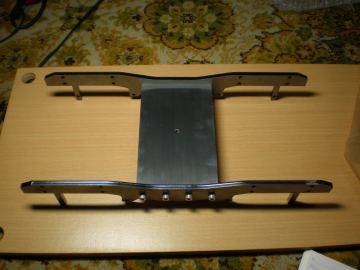 両側取り付けてH型枠になりました。
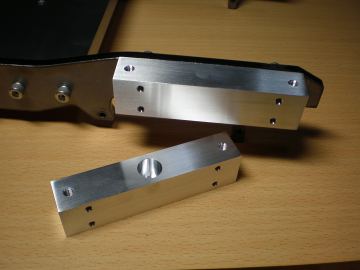 バネで荷重を受ける角材部品をボルト止めしていきます。 ここには車輪とのクリアランスを大きくとるため、 低頭キャップボルトを用います。
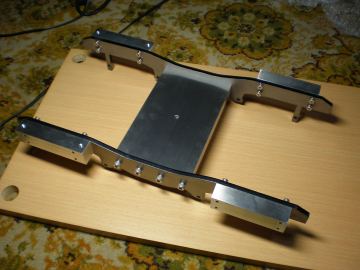 4箇所付け終わりました。
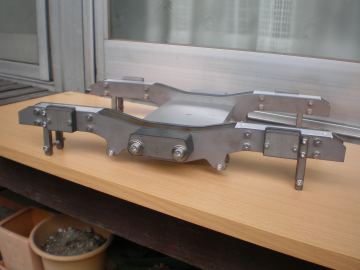 ※この画像はクリックで拡大できます 上記に外側フレームを取り付ければ主台枠の完成です。
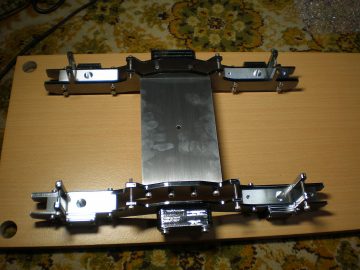 裏側より。
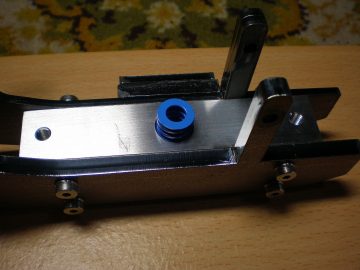 バネはこのように収まります。 約3mmのプリロードをかけ、整備重量1G状態で約1mmの伸び、 約4mmの縮み幅があるように設定しました。 スペーサーなどを挿入すればバネ変更、プリロード変更も可能です。
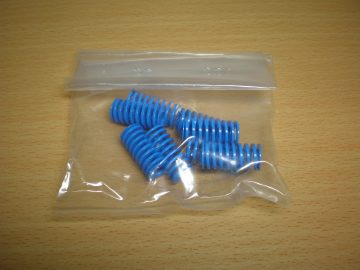 今回使用したバネです。 『東京発条製』"TL12×25"で、バネ定数は20.7N/mm。
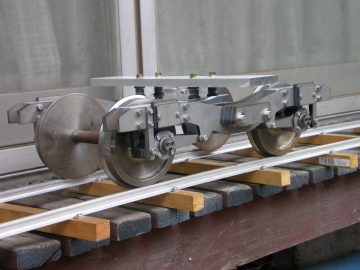 ※この画像はクリックで拡大できます ベアリングを入れたスイングアームと車輪を組めばひとまず完成です。 今のところ長期在庫している仮車輪をつけてあります。 部品が揃い次第動力台車化する予定です。
|
|
|
2007/02/15更新
| | 新台車試作3
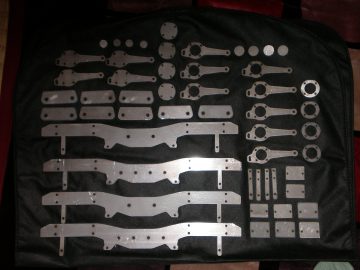 台車主枠部品のレーザーカットが出来上がってきました。 曲線をきれいに表現できるのがなんともいえません、感無量です。 施工は広島スチール工業さんにお願いしました。 『【鉄道模型】など個人向けマニアのための試作対応! 』というのが頼もしい限りです。
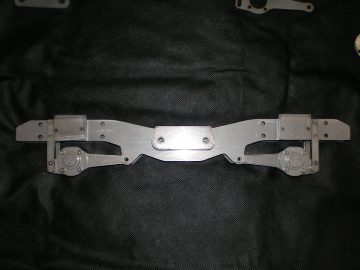 ※この画像はクリックで拡大できます. ためしに並べて(重ねて)様子を見てみました。 それらしくなったでしょうか?
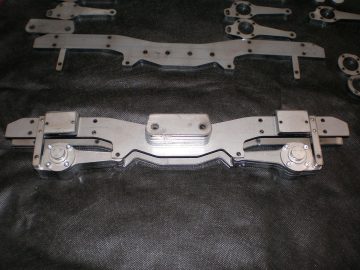 ※この画像はクリックで拡大できます 斜めから見ると構造が分かると思います。 全て2種類の板材で製作するための苦肉の策です。
|
|
|
2007/02/07更新
| | 新台車試作2
部品図面が出来上がりましたので、必要数を全て並べてレーザーカットを依頼しました。6.0tと3.2tの2種類を用いることにしました。
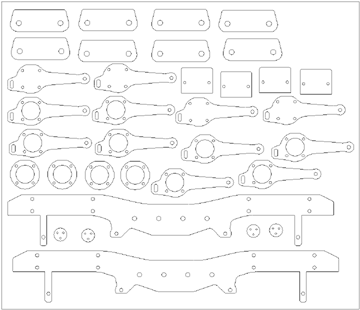 こちらは6.0tの部品群
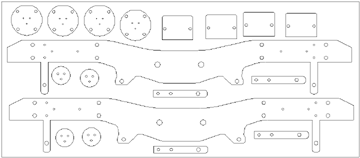 続いて3.2tの部品群
以上の2枚で1台車分です。
|
|
|
2007/01/24更新
| | 新台車試作
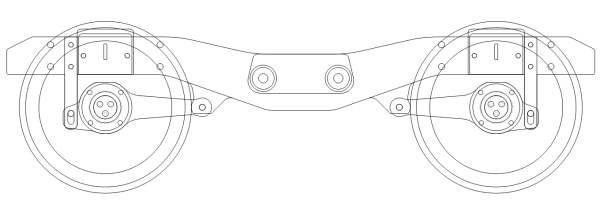
当初は簡素な実用台車を履かせると決めていましたが、倶楽部の方々の車両をいろいろ見ているうちにちょっと凝ったものが作りたくなってしまいました。 とりあえずは今までの構想通り棒材と板材のH型簡易台車で製作を進め、並行して各所同一寸法の台車を試作することにしました。試作品が完成次第簡単な走行テストを行い、換装してみることにします。 モデルにするのはJR東日本のDT74,TR249台車です。軸梁式の台車で、EF210のそれにもつながるかなということで決定しました。レーザーカットした板材と、穴あけ・タップ加工した棒材・板材を組み合わせる構造を考えています。軸受けにはニードルローラーベアリングを使用予定です。 台車搭載部品の互換性を持たせるため、寸法や追加孔等実物とは著しく異なりますが、とりあえずこのまま進めてみます。
|
|
|
2007/01/14更新
| | エンジンマウント兼ギアボックスの製作
頼んであったシャフトが出来上がってきたので製作再開です。
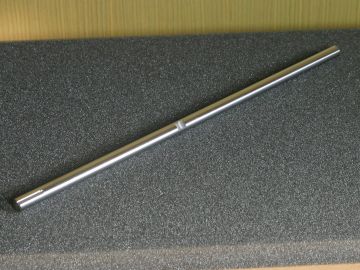 ギアボックスに用いるシャフトが到着しました。 製作は『協栄ホーニング』さんにお願いしました。 軸径は10mmです。
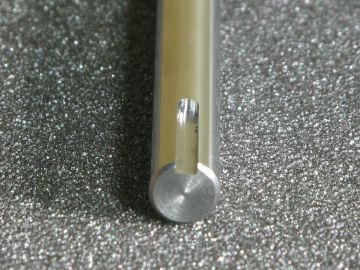 先端はスプロケットを取り付けるため、3×3用のキー溝加工がしてあります。
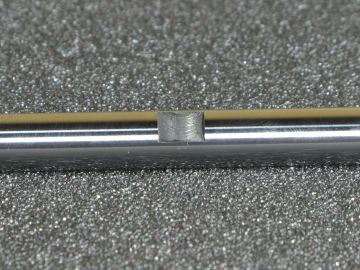 中程にはギア止めねじ用のDカット加工がしてあります。
 軸周りの構成部品。 部品の詳細は、「06/12/01更新」・「06/12/17更新」に記載してあります。
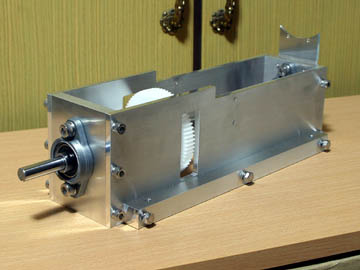 先日組んだフレームに取り付けました。
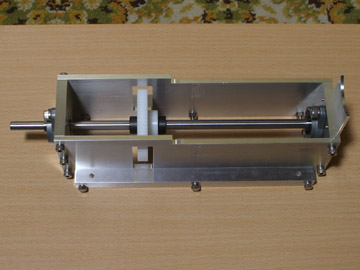 ※この画像はクリックで拡大できます 上から。
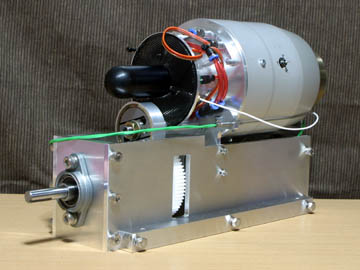 ※この画像はクリックで拡大できます エンジンを載せて噛み合い確認です。 バックラッシュは紙を挟んで調整してみました。 まずはこの状態で定格運転させてみて様子を見ることにします。
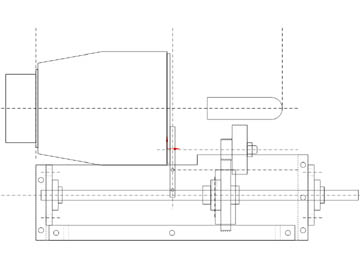
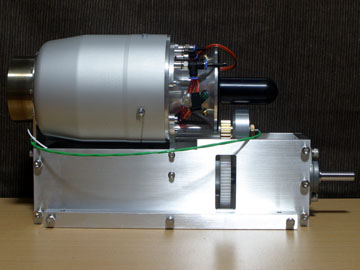 ※この画像はクリックで拡大できます 図面とならべてみたました。 このシステムでタービン回転数を約1/18に減速します。 あとは防振ゴムを取り付けて、リアサポート用のM2.5キャップボルトが到着すれば完成です。 |
|
|
2007/01/11更新
| | ボルスター製作
部品が揃ったので製作開始です。
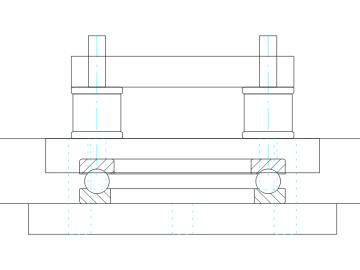 ボルスターの構造です。 防振ゴムを板で挟み、台車との接合部にスラストベアリングを入れるだけの簡素なものです。
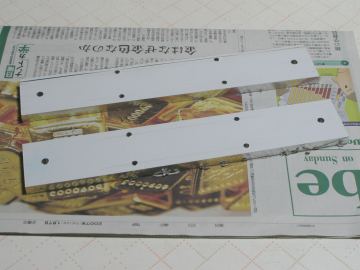 ボルスター上部です。 材質はA5083アルミ板、入手先は台枠横梁と同じく『とくきん』です。 孔あけのみで完成。
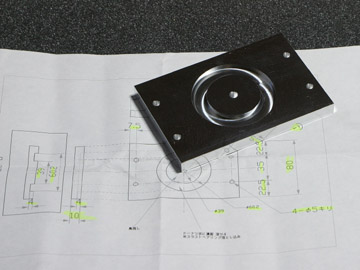 ボルスターの下部です。 センターにスラストベアリングを落とし込む構造にしたかったので、 加工は『アルミプラス』さんにお願いしました。
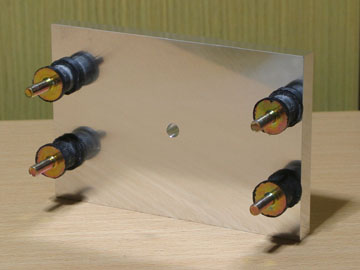 ボルスター下部に防振ゴムを組み付けます。 部品は倉敷化工製丸型防振ゴム"RA-15"。
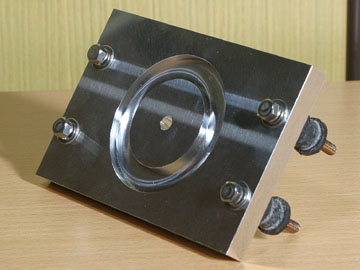 反対側から。
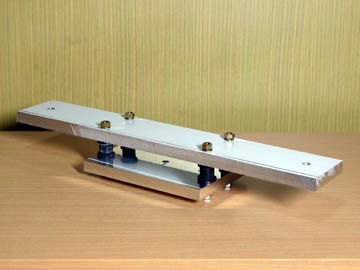 防振ゴムを上下部で挟めばすでに完成。単純です。 ですが今はまだ仮組みです。 本組のときにもう1つ作ります。
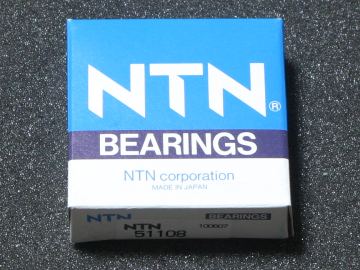 今回用いるスラストベアリング、『NTN』製"51108"。
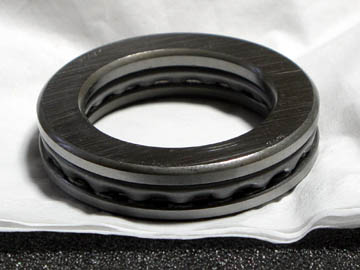 これを下部の溝に落とし込み、台車と挟んで使用します。
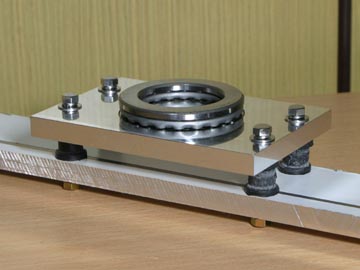 溝に落とし込んでみました。ぴったりです。 このようなベアリングは荷重しないと分解してしまうので実際の使用状態と上下逆で撮影。 |
|
|
2007/01/01更新
| | ターボシャフトエンジン到着
明けましておめでとうございます、元旦から更新です。 本プロジェクトの要、『Jakadofsky』製ターボシャフトエンジン(PJ-W Turboshaft Engine RS)が到着しました。
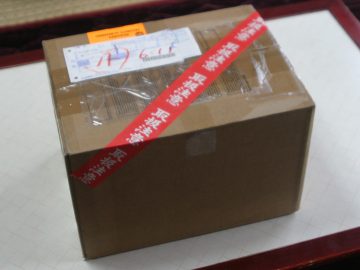 オーストリアから、神戸の代理店『フォックスコーポレーション』経由でやってきました。
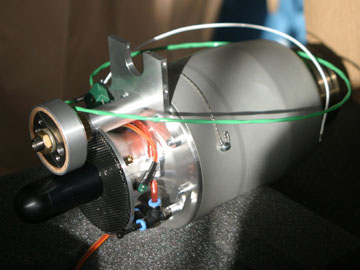 早速開封してみました。 やはりすごく軽いです、この小ささで4kwを発生するとは...。 はやく火を入れてみたいところですが、R/C装置がまだ無く、 エンジン廻りの小物も揃っていないため当分先になりそうです。 マニュアルも案の定英語なのでセッティングにも時間がかかるかもしれません...。
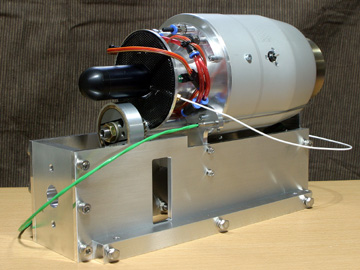 ※この画像はクリックで拡大できます マウント兼ギアボックスに組みつけてみました。 孔位置もばっちりです。 あとは軸が揃えば一通り完成です。
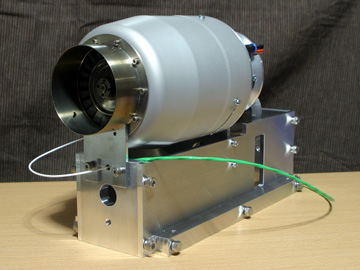 ※この画像はクリックで拡大できます 排気側から。 エンジンは前部のフランジ部とリアサポートで支えられています。 |
|
|
2006/12/30更新
| | エンジンマウント兼ギアボックス部品到着
エンジン出力取り出しに関わる大事な部分ということで加工をお願いしていたものが出来上がってきました。図面を送って、製品になって帰ってくるというのは僕自身にとって大変新鮮でした。加工品の方もさすがはプロ、単純な部品でも感動ものです!
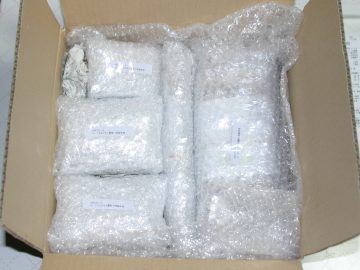 厳重に梱包されてやってきました。 加工をお願いした先は『アルミプラス』さんです。
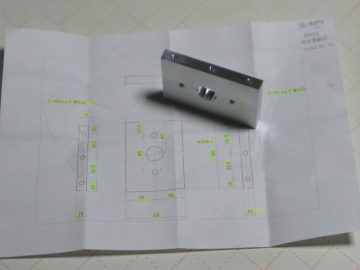 自分でひいた図面からたった1つだけでも安価で作ってくれます。 大変ありがたいです。
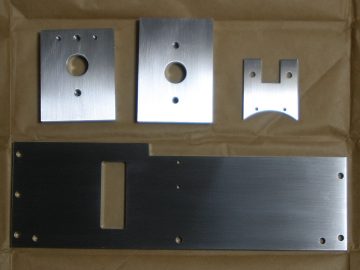 ギアボックスを構成する部品群です。 板材はA5052、棒材はA6063、それぞれアルミ材料を使用しています。
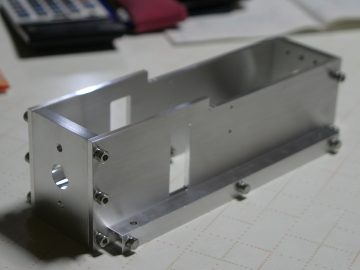 早速仮組みしてみました。 すばらしい! 早くエンジンを載せたいですね。
台車用アルミ素材到着&加工開始
 台枠側梁用のアルミ角棒材が到着しました。 早速図面通りに位置を記して加工準備に取り掛かります。 A6063の20×20を『ニッカル商工』にて一本定尺(4m)購入して公差±0.5で切って納品してもらいました。個人で尚且つ極少量でしたがいろいろ相談に乗ってもらえ、ありがたかったです。 必要なのは4本ですが、残材の問題と後々の台車に使えるということで8本分切ってあります。 このような少量でもやはり定尺購入が一番安上がりなんですかね...。
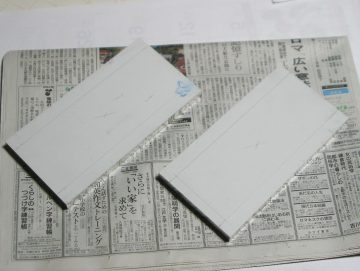 こちらは横梁用の板厚12mmA5058アルミ。表面が白くみえるのは保護シートが貼ってあるからです。 最初は角材を使用する予定でしたが、少量にもかかわらず定尺購入となり価格が現実的ではありませんでした。ということで板材から安価に切り出してくれるところを探して入手しました。 入手先は『とくきん』です。アルミに限らず鉄・非鉄各種取り扱ってもらえるようです。
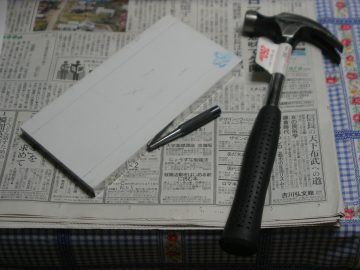 保護シートの上からですが、ポンチを使ってセンターを打刻します。
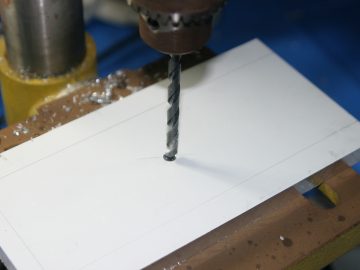 10年以上前のホームセンター品ボール盤ですが十分間に合います。 今現在も加工途中です。 |
|
|
2006/12/17更新
| | 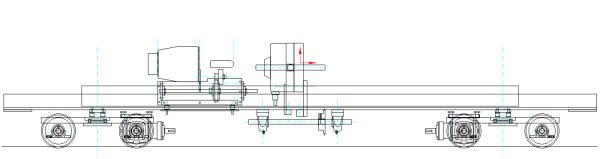 配置
全体の大まかな寸法・配置等が決まりました。
○寸法 フレーム長が1,900mm、ボギー中心距離1,300mmで、7.5R通過時の台車ヨー角は約5°です。このサイズは実車でいうと大体16m級でしょうか、JR東日本のキハ100系ほどの大きさになる予定です。フレーム基準床面高さは120mmで、床下センターを走るドライブシャフトはキハ8500よりも高い位置に配置し、大径のスプロケットにも対応できるようにします。
○フレーム構造・材質 キハ8500の鋼製アングルフレームは重たくがっちりしているように思えますが、センター付近に配されたエンジンとトルコンの重みで反ってしまっていました。これは車両を正面よりみると明らかで、それにつられて3分割ボディーも真ん中が落ち込んでいるというみっともない格好になっています。今回はこのような事態は避けたいので、軽さと強さ(特にボギー間)を併せ持つような性能を持たせたいと思っています。素材はキハ8500よりも寸法、厚み共上回る等辺アルミアングルを用い、ボギー間を平角材で補強する方向で検討中です。とりあえず中央に来る重量物もボギー間もキハ8500より少なく短いので、もう少し軽くて運びやすい車両を目指します。
アクシデント!
想定外の事が起きてしまいました。今回また使う予定のトルコンを製造していたアメリカの会社が倒産し、入手が非常に困難な状況だそうです。現在生産・流通在庫がないか探してもらっています。どうしても入手不能な場合は、別会社の効率の高いモデルを使用するか、キハ8500に搭載しているものを降ろして使おうかと考えています。現状では前者が非常に高額のため、後者を選択してキハ用のミッション探しor自主開発をする道が濃厚です。 ※このトルコンを使用することを前提で各種制御系を考えてきましたので、今回の車両に新たなミッションを載せる事は考えません。
台車の材質
やはり台枠が鋼製では軽量化できる分は微々たるもので、『運びやすい車両にする』ということに貢献できそうにありません。ということでアルミで製作することにしました。例によって規格材を寸切りでそのまま使用するため、角材ラインアップに合わせて各所寸法を小変更しました。 ちなみにキハ8500の鋼製台車は1つ17kgあります。参考までに×8.4^3すると10t超えてしまいます。重すぎですね。
トルコン制御
今回トルコンの制御レバーをサーボモータで動かしてやろうと決めたので、早速試してみました。
○サーボ トルクはラジコンの一般的なハイトルク型サーボで十分なのですが、その制御が課題になりました。どうせエンジン制御用にR/C装置を載せるのだから、それの1chを使えばいいところですが、今後、レシプロエンジンのスロットル制御などにも応用したいため、別系統(R/C装置なし)で動かすことにしました。
○制御装置 マイコンなどを使って自作されてる方(今流行っている人型ロボット用)を参考に作ろうかと考えていたところ、利根川精工製の『インテリジェントサーボコントローラ』というのを見つけました。この発見で自作は即後回しになりました...。これはサーボの位置制御に必要なパルス信号幅を入力電圧(ボリュームで制御)によって変化させてくれます。
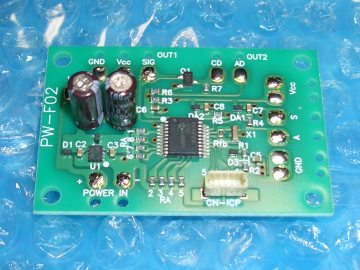 利根川精工製『インテリジェントサーボコントローラ』
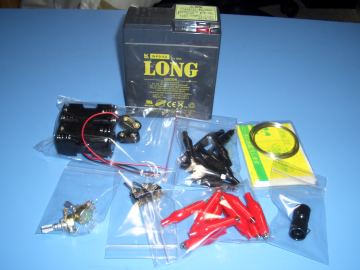 必要部品は秋月電子通商から調達。 あまり秋月らしいものを買っていませんが...。
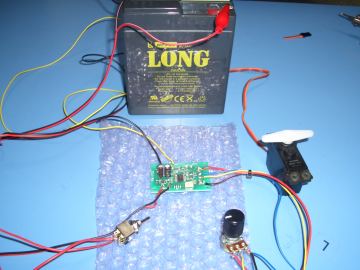 早速配線して動作確認しました。問題なく動いたのですが、動作角が±約45deg.と、随分少ないものでした。入力電圧の問題なのかサーボの仕様なのかこの手のスキルが低くまだわかりません..調査してみます。(写真のサーボはテスト用でJR製NES-511.このコントローラは基本的に動作用別電源回路を持ったサーボ用で、サーボを稼動させるような電力は供給できない仕様でした。ということなので、別電源回路を追加して動作させています。)
部品調達状況
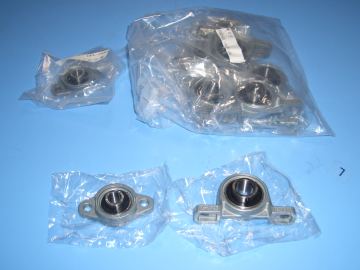 エンジンギアボックス用・台車軸用ピローユニット到着.
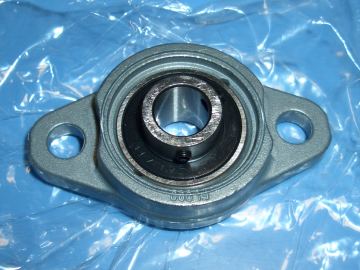 エンジンユニット用軸受け. FYH(日本ピローブロック)製ひし形ベアリングユニットUFL000,軸穴φ10.
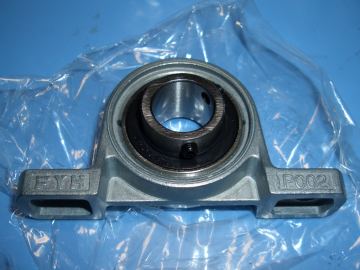 台車用ベアリングユニット. 同じくFYH製UP002ピローユニット.軸穴φ15.
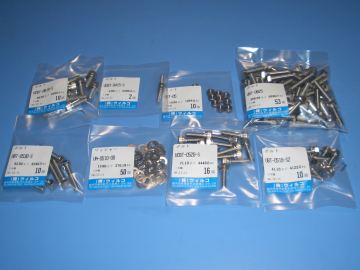 ねじ・ボルト類は、ばら売りしている最寄のDIY店でいつも購入するのですが、今回使用する一部をネット販売(ウィルコ)にて調達してみました。製品ごとに細かく小分けされていて、いざ使うときに便利そうです。 単価ですが、やはり大量購入に向いています。少量だとDIY店のほうが安いです。しかしながら特殊なものが必要な時には頼りになるかもしれません。
|
|
|
2006/12/9更新
| | 制御系
○エンジン制御 エンジンの制御のほとんどは専用のECU任せのようです(まだ到着していません.輸入してくださるところにいろいろお尋ねしました)。始動もフルオートで、スイッチオンのみ!レシプロエンジンのキャブ調整やニードルセッティング等、根気のいるようなことも全くする必要がありません。ですが、エンジン始動、アイドル・定格運転の切り替え、停止といった基本的な指令は出してやる必要があります。(当たり前ですが...) このエンジンは元々R/Cヘリコプター用に開発されたものですので、上記のような制御もR/C装置と連動するようにできています。そのため、一番手っ取り早く車両にインストールするにはヘリ用RC装置を載せてしまうことでした。用いるチャンネルはスロットルとギアやAUX等1ch、機能としてはスロットルホールド(アイドルアップ)を装備していることが条件だそうです(もちろんサーボはいりません)。ということで、今のところ一番ベーシックなヘリ用6chを積む(送信機・受信機のみ)予定でいます。自身もヘリを飛ばしていましたので、昔のでも使えそうなものを物色しています。 最後に電波に関してですが、このようなR/C装置の使い方で電波を出してしまうと、混信によって周りの方々(近くでR/Cを飛ばしている方)に迷惑をかけてしまったり、自機が暴走する可能性があるため、D.S.C.を用いて電波を出さずに稼動させます。
○車速制御 今回もクラッチ・変速機・逆転機能を装備したトルクコンバータを使用しますので、車速制御はキハ8500同様レバー1本です。しかし、キハ8500ではレバーが機械式直結であったため、運転台が動力車側にあり、あまりスマートではないような気がしていました。実際、曲線通過などでは運転台が移動して運転しにくいということもありました。 ということで、今回はトルクコンバータの出力制御をサーボを使って行おうと思います。これであれば、実際の運転に関わる部分(車速・ホーン・ライトなど)はスレーブユニットに搭載して、客車で操作できるようになります。
|
|
|
2006/12/1更新
| |
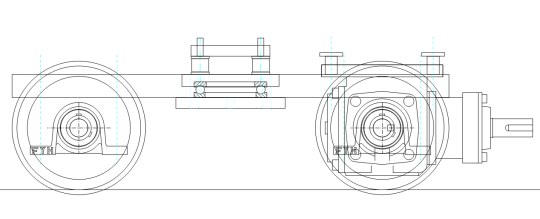 台車設計中
基本設計はキハ8500と同等です。全く実車を意識していません。単純・簡素であり、台車としての性能重視です。 当初両軸駆動にしようかとも思いましたが、軸距離250mmだとスペース的に厳しいのと、台車にかかるコストが3倍近くになってしまう(通し軸のギアボックスが高価&ベベルボックスの自作は今回もしません)ので1軸駆動です。実車でもディーゼルカーの多くは2/4駆動なのでまぁよいとします。 キハ8500の台車と異なる点としては、ボルスターに防振ゴムを組み込んだ設計にしたことが挙げられます。これによって台車の振動がエンジンにより伝わりにくくなり、加えて軌道不整にもよく対応してくれると思います。また心皿部にはNTN製のスラストベアリングを入れ、台車の円滑な動作を可能にします。軸箱支持用バネ・ベベルボックス支持用バネのレートも共に見直しています。必要以上の鋼材の厚みを無くし、各所軽量化を図る予定です。
加工依頼
エンジンユニットは設計も終わり、後は実際に製作するだけなのですが、これを構成する部品を製作するには各種機械加工が必要(金鋸や小型ボール盤でも不可能ではないですが気が遠くなります)で尚且つ精度もほしいところです。今のところ自分には切削機械も腕もありませんので、加工を依頼することにしました。(というよりお願いできそうなところを見つけたので、それにあわせて設計を進めました..) 依頼先は個人向けのアルミ加工を行っている『アルミプラス』(運営:小池製作所)というところです。図面をメールで送ると直ぐに見積もり結果を返送してくださり、いろいろなアドバイスもいただきました。現在正式に発注して納品待ちです。納期は約4週間とのことでした。
部品到着
注文していたエンジンユニット用の部品が到着し始めました。
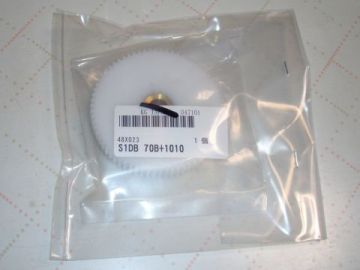
"平歯車-ポリアセタール-黄銅ブッシュ入り,モジュール1,歯数70,型番S1DB 70B+1010"
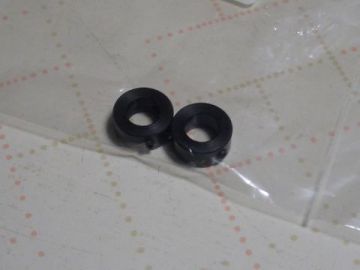
セットカラー : 歯車が軸方向に動かないように固定するために使います。
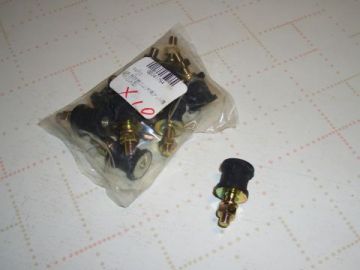
防振ゴム : 数が多いのは台車にも使用するためです。
|
|
|
2006/11/25更新
| | 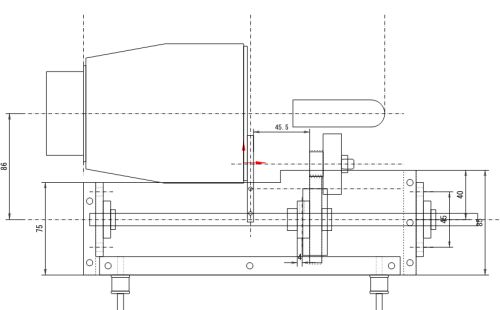
エンジンマウント兼ギアボックスの設計
○動力伝達の流れ このエンジンはタービン機関である故、減速された出力軸でさえかなりの高回転になります。そのため大きな減速比が必要になりました。そのため、伝導の流れとして、エンジン→(ギア)→二次減速軸→(チェーン)→トルコンという形をとることにしました。エンジンの出力軸にあるクラッチベルにはモジュール1のギアが使われているため、これにあわせたギアボックス製作をしていきます。
○ギア比の決定 まず各所回転数を決めなれればばなりません。今回使用予定のトルクコンバータの最大入力回転数は3,600rpmということですが、キハ8500のときにmax3,000rpm程で入力させていたため、これと同じ使い方をすることにしました。エンジンの諸元表より、定格出力時のクラッチベル回転数は17,400 rpmなので、1/6程に減速することになります。このギアボックスでは2箇所で減速(エンジン出力-二次減速軸-トルコン入力軸)できるので、ボックス全体のサイズや配置を考えながらギア比を決めていきます。
トルコンへの入力(最終減速)にはチェーンを用いる予定なので、これ以前でできるだけ大きく減速してやることにしました。となると二次減速ギアを可能な限り歯数の多いものを選べばいいのですが、エンジンマウントの設計上大きさに制限ができてしまい、歯数70に決定しました。エンジンのピニオンギアの歯数はできるだけ少なくということで、選べる最少の20にします。噛み合うギアの歯数が互いに素ではなくなってしまいましたが、問題が出れば即交換と考えることにします。このギア比により二次減速軸は約5,000rpmに落ちました。あとはスプロケットにて約1.6の減速比を得ればよいのですが、用いる歯数はトルコンの軸配置によって変えたいので決定はフレーム全体の設計時にします。
○部品・素材 ・ギアボックス 構造は板に角材を挟んだ直方体で、素材はアルミを使うことにします。エンジン自体の振動はかなり少ないと思いますが、チェーン・トルコンからの振動をどうしても受けてしまいますので、マウントには防振ゴムを装備します。
・歯車 協育歯車工業製で、材質はポリアセタールという樹脂です。本エンジンが本来の用途であるラジコンに搭載されるとき、使われるギアが樹脂でしたのでこれにします。 "平歯車-ポリアセタール-黄銅ブッシュ入り,モジュール1,歯数70,型番S1DB 70B+1010"
・軸 φ10の汎用シャフトを加工(Dカット・キー溝)してもらい使用予定です。
・防振ゴム 倉敷化工製丸型防振ゴム"RA-15" |
|
|
2006/11/18更新
| | 全体の大まかな構成について(ii)
○パワートレイン アイドリングさせる必要のある熱機関を5インチゲージ車両の動力源として使うとき一番苦労するのがパワートレイン(特にクラッチとトランスミッション)ではないでしょうか。 幸いなことに以前製作したキハ8500のメカニズムでよいデータが取れていますので、今回もこのシステムを踏襲することにします。具体的には、クラッチ・変速・逆転機構をトルクコンバーターで一括して賄い、フレーム本体から台車・車軸への動力伝達は伸縮機能付自在継手とベベルギアボックスによって行う予定です。 変速機や逆転機を自作するのも大変面白そうですが、今回はガスタービン動力で走ることに重点を置いていますので後回しにします。
○台車 台車も基本設計はキハ8500のものを使う予定です。性能も満足できるレベルのもので、今まで何度も高速でポイントや曲線を通過しましたが脱線したことは一度もありません。ただ、今回はメインフレームの剛性を上げるつもりですので、防振ゴムを用いたゆれ機構を取り入れる予定です。 素材は悩みどころです。キハ8500のあの鋼製台車は重くて車両の扱いを困難にした要因であったのでアルミにして軽くしようかとも考えていますが、台車はフレームからはずして運搬することができる場所であり、絶対的な剛性も必要ですので鉄のままでもよいかな、とも考えています。台車設計時に決定することにします。
設計の流れ
エンジンの軸出力を使いやすい(一般のスプロケット等を使える)ように取り出すためのギアボックス(マウント一体型のエンジンユニット)を中心に考えていますので、そのスペックによって構成部品全てのそれが変わってきます。ですのでこのギアボックスの設計が終わり次第、他の構成部品の詳細を決めていきます。 |
|
|
2006/11/17更新2 | | 全体の大まかな構成について(i)
○エンジン R/Cヘリ用のターボシャフトエンジンを使用する予定です。というより、このエンジンが市販されるようになったので製作を思いついた、というのが本当のところです。 僕がはじめてラジコン用のタービンエンジンの存在を知ったのはもう十数年前でしょうか、ラジコン技術という雑誌に"ターボレックT240"というターボジェットエンジンを積んだ機体が紹介された時です。以来海外メーカーを中心に開発が活発化し、数年前(多分)にはスラストではなく軸出力を取り出した"ターボシャフトエンジン"が作られ、ラジコンヘリもJetの時代がやってきました。
実際に搭載する機種も決定しました。Jakadofsky社製の"PJ-W Turboshaft Engine RS"というターボシャフトモデルです。定格軸出力は4kW,約5.5馬力(タービン回転数89,000rpm)で十分すぎる性能を持っています。一番の注目点は出力というよりその重量で、5馬力以上を発生する機関でありながら僅か1300gしかありません。同じくらいの定格出力を持つ一般的な汎用レシプロエンジンですと20kg以上になるため、ガスタービン機関の小型軽量高出力という特徴がよくわかります。また、ピストンエンジンと異なり往復運動する部品がないため振動の発生がきわめて少ないというのもガスタービン機関の特徴です。
ガスタービン機関の欠点に燃費が悪い(熱効率が低い理論サイクル)というのがありますが、できるだけ全開状態で動かしてやればよい効率が得られる(アイドリングでの燃料消費量は全開時に比べてきわめて大きい)のと、大量の燃料を搭載する場所は確保できそうなのでこの点に関しては目をつぶります。(※お世辞にも環境に優しいとはいえませんが、排気ガス中に含まれる窒素酸化物などはレシプロ機関より少ないようです.) 何よりどんなエンジンだろうと出力に見合った燃料を食わなければ働かないのでしょうがないですね。
高出力エンジンを搭載するということなので、ここでちょっとスケール換算をしてみます。 今回搭載予定の機関定格出力は4kWということなので、単純に(8.4)^3をかけるとスケール出力約2,370kWということになります。(もちろん材料を構成している原子も1/8.4縮尺できるわけではないのであくまでも概算です.そういえば5インチゲージで出力・重量もスケール換算して作られてる方は少ないんじゃないでしょうか.) 実車で一両あたりの出力が2,370kWとなりますとこれは間違いなく機関車に相当します。EF81型電気機関車の交流区間での1時間定格がちょうどこれくらいみたいですので、相当なハイパワー気動車ということになりそうです。
【参考文献】 フリー百科事典『ウィキペディア(Wikipedia)』熱機関の理論サイクル・電気機関車 |
|
|
2006/11/17更新 | | 本日ガスタービン動車プロジェクトWebを始動させました。 実際、構想自体は4〜5年前から抱いていて、実現させる見込みが出てきたのでwebにて公開しようと決めました。これから構想や実際の製作記などを載せていきたいと思います。
〜本プロジェクトの基本コンセプト〜 1.ガスタービン機関で走ればよい 2.できるだけ市販品を使う 3.軽トラの荷台にはみ出さず載る
まず1.についてですが、これは実車を忠実に再現するつもりは特に無いということです。仮にキハ391を製作ということになると3両1セットですし、連接・振り子といったギミック満載です。せっかく作るなら全部再現したいので、とりあえず今回は形式指定を特にしません。
次に2.についてですが、自身の方針として完全自作(部品製作のほうです、設計は自分でします)を掲げてはいませんので、少々金額がかかっても信頼できる既製品(機械部品)を多用する予定です。新規性と目の付け所で勝負といったところでしょうか。究極のディテールより構造・機構で凝ったものや新しいもの作るということに重点をおきたいと考えています。(キハ8500ボデーの出来の悪さがそれを物語っていますね...)
最後に3.ですが、これは重要なことで、大きくて重い車両は当然のごとく運搬で苦労します。キハ8500(20m級フルサイズ)でいろいろ大変な思いをしていますので、今回は短めの車両(16m級)を考えています。これですと軽トラックの荷台にすっぽりと収まります。短ければ車重も減らせますし、曲線通過にかかわる各所への負担も減らせます。ボギーをやめればいいというのもありますが、搭載しなければならない装備が多いため2軸車は考えていません。 |
|
|